3D 프린팅 기술(적층 제조라고도 함)은 혁신적인 제조 방식입니다. 3D 프린팅 재료를 층층이 쌓아 3차원 물체를 제작합니다. 디지털 모델 파일을 기반으로 합니다. 물체를 얇게 자른 후, 금속 분말, 수지, 플라스틱 또는 세라믹과 같은 재료를 FDM(용융 적층 모델링), SLA/DLP(광 경화), SLS(선택적 레이저 소결) 등의 공정을 통해 층층이 쌓아 올립니다. 기존의 금형이나 가공 없이 복잡한 구조물을 직접 제작할 수 있습니다.
로봇 공학 분야의 최첨단 기술로서, 휴머노이드 로봇은 핵심 부품의 정밀성, 경량성, 그리고 기능성에 대한 매우 높은 요구 조건을 충족해야 합니다. 기존의 제조 공정은 복잡한 구조를 다룰 때 높은 비용과 긴 제작 주기와 같은 문제에 직면하는 경우가 많습니다. 유연성과 효율성을 갖춘 3D 프린팅 기술은 복잡한 관절 구조, 경량 부품, 그리고 고정밀 센서 하우징을 신속하게 제작할 수 있습니다. 3D 프린팅은 휴머노이드 로봇의 성능과 신뢰성을 크게 향상시키고 로봇 제조에 새로운 가능성을 제공합니다.
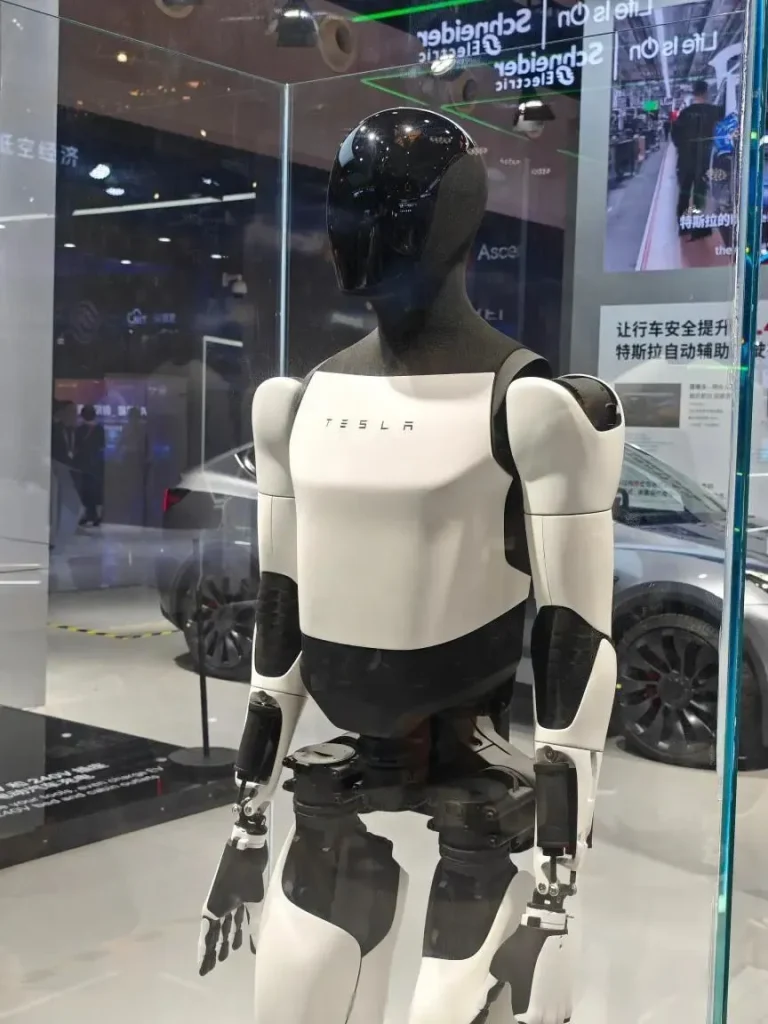
가볍고 고성능: 3D 프린팅 소재의 핵심 혁신
휴머노이드 로봇의 동작 효율, 에너지 소비 제어, 그리고 동적 안정성은 소재의 경량화 및 기능적 통합에 크게 좌우됩니다. CNC 가공이나 사출 성형과 같은 기존 제조 공정은 복잡한 구조 통합 및 경량화 설계에 어려움을 겪습니다. 3D 프린팅 기술은 소재 혁신과 구조 설계 혁신을 통해 체계적인 솔루션을 제공합니다.
1. 금속 분말: 경량 골격의 초석
티타늄 합금(Ti6Al4V)과 알루미늄 합금(AlSi10Mg)은 로봇 하중 지지 구조물(흉골 및 관절 커넥터 등)에 가장 많이 사용되는 소재입니다. 높은 비강도, 뛰어난 내식성, 그리고 생체 적합성을 갖추고 있습니다. 티타늄 합금(4.5g/cm³)의 밀도는 강철의 57%에 불과하지만 강도는 비슷합니다. 알루미늄 합금(2.7g/cm³)은 우수한 열전도도를 유지하면서 무게를 더욱 줄여줍니다.
국내 티타늄 분말 가격은 2024년 kg당 600위안에서 2025년 kg당 300위안 미만으로 50% 하락했습니다. 이러한 획기적인 발전은 지능형 생산 공정 개선(분말 수율 향상을 위한 아르곤 회수 기술 등)과 Willari와 같은 기업의 대량 생산 덕분입니다. 테슬라 옵티머스 Gen2를 예로 들면, 무릎 지지 구조는 3D 프린팅 티타늄 합금을 사용하여 무게를 42% 줄이고 충격 저항성을 향상시켰습니다.
2. 특수 복합소재: 역동적인 성능의 혁신
3D 프린팅 소재는 다음과 같은 특징을 가지고 있습니다. 볼리 테크놀로지(Boli Technology)에서 개발한 다층 허니콤 복합 소재(TPU 엘라스토머 기반)는 생체 조직의 완충 메커니즘을 모방합니다. 허니콤 다공성 구조는 충격 에너지를 흡수하고, 100만 회 이상의 굽힘 강도를 견딜 수 있으며, 45MPa의 인열 강도와 98% 이상의 탄성 회복률을 보입니다. 이 소재는 팔꿈치 및 무릎 완충층에 사용되어 기존 금속 리미터를 대체하고, 70%로 관절 움직임의 자유도를 높이며, 금속 부품의 충돌 손상을 방지합니다.
경량성: 벌집 구조의 다공성은 조절 가능하며, 밀도는 0.6-0.9g/cm³에 불과하여 동일한 부피의 알루미늄 합금보다 60%가 더 가볍습니다.
방열 향상: 다공성 구조는 방열 표면적을 늘리고, 높은 열전도도 필러(예: 질화붕소)를 사용하면 40%의 열전도도 효율이 증가하여 조인트 모터의 작동 온도를 효과적으로 낮출 수 있습니다.
에너지 피드백: 이 소재는 압축-반발 과정 동안 운동 에너지를 저장하고 방출하여 로봇 운동의 에너지 효율 비율을 개선합니다.
3. 엔지니어링 플라스틱: 유연한 기능 통합의 핵심
PEEK(폴리에테르에테르케톤)는 뛰어난 성능적 이점을 제공합니다. 밀도가 1.3g/cm³(마그네슘 합금의 약 절반), 인장 강도가 100MPa, 내열성이 최대 260°C, 마찰 계수가 0.1~0.3(자체 윤활)이며 생체적합성이 우수합니다.
항저우 디앤쯔 대학은 3D 프린팅 PEEK를 사용하여 로봇 관절 베어링을 생산하여 금속 베어링에 비해 50%의 무게를 줄이고, 내마모성을 3배 높이고 윤활유가 필요 없게 되었습니다.
적용 분야 확장: 테슬라의 Optimus Gen2에서는 PEEK가 척추 지지 구조와 기어의 알루미늄 합금을 대체하여 로봇의 전체 중량을 10kg 줄이고 이동 속도를 30%만큼 향상시켰습니다.
응용 분야 | 기술적 이점 | 대표 사례 | 달성된 결과 |
구조적 구성 요소 | 복합 구조가 일체적으로 형성됨 | BLT-SLM 인쇄 어깨 브라켓 및 흉골 | 30% 무게 감소, 50% 조립 단계 감소 |
생체 조직 | 다중 소재 유연 인쇄 | 그림 02 벌집형 조인트 버퍼층 | 향상된 유연성, 연장된 수명 |
센서 제조 | 정밀 미세 구조 통합 | BLT 6D 힘 센서 “포톤 핑거” | 세계 최소형(mm급), 40% 비용 절감 |
열 관리 | 토폴로지 최적화 채널 설계 | 인간형 로봇 모터 냉각 구조 | 15°C 온도 강하, 20% 내구성 향상 |
기술 강화: 프로토타입 설계부터 대량 생산까지
3D 프린팅 기술은 인간형 로봇 연구 개발의 모든 단계에서 핵심적인 역할을 합니다.
1. 신속한 프로토타입 제작 및 반복
3D 프린팅의 금형 없는 특성은 설계 및 반복 주기를 최대 100% 단축합니다. 70%.
예를 들어, "징추(Jingchu)" 휴머노이드 로봇은 2025년 2월 이후 4개월 동안 네 번의 반복 작업을 거쳐 서비스 지향형 모델과 산업용 모델로 구분되었습니다. 관절의 각 구조 최적화는 3D 프린팅 프로토타입을 통해 가능했습니다.
2. 복잡한 구조물의 제조
선택적 레이저 용융(SLM) 및 기타 3D 프린팅 기술을 사용하면 30%만큼 무게를 줄이고 구조적 무결성을 유지하며 모터 과열을 방지하기 위해 통합된 방열 채널을 통합한 내부 격자 설계로 위상적으로 최적화된 구조가 가능합니다.
3. 기능 통합 및 혁신
센서 퓨전:
3D 프린팅은 마이크로 센서를 로봇 구조에 직접 통합하여 부품 수와 조립 복잡성을 줄이는 소형 다기능 구성 요소를 구현할 수 있습니다.
열 관리 설계:
모터 주위에 격자형으로 설계된 냉각 채널이 최대 작동 온도를 최대 15°C까지 낮추어 모터 수명을 연장하고 에너지 효율을 향상시킵니다.
EPIC Powder Machinery의 분말 생산 지원
고성능 3D 프린팅 소재의 핵심은 초미립, 고순도 분말입니다. 에픽 파우더 기계는 다음을 제공합니다. 제트 밀링 이를 가능하게 하는 시스템입니다. EPIC의 유동층 제트밀은 적층 제조에 사용되는 초미립 금속 분말(예: 티타늄 합금, 알루미늄 합금) 및 엔지니어링 플라스틱(예: PEEK, PPS, PA) 생산에 이상적입니다.
높은 구형도와 좁은 입자 분포로 분말 베드 용융 및 SLM 공정에 이상적입니다. 반응성 금속 및 폴리머에 세라믹 또는 내마모성 라이닝을 사용하여 오염을 최소화합니다. 항공우주 및 로봇 산업의 엄격한 기준을 충족하는 일관된 배치별 품질을 제공합니다.
비용 절감 및 효율성 개선: 산업화 추진
3D 프린팅은 비용을 절감하고 제조 효율성을 개선하여 산업화를 가속화하고 있습니다.
재료비 절감:
티타늄 분말 가격이 kg당 600위안에서 300위안으로 하락했습니다. 금속 분말이 3D 프린팅 총비용에서 약 17%를 차지하는 것을 고려하면, 이러한 가격 하락은 부품 수준의 비용 효율성을 크게 향상시킵니다.
왜 EPIC 분말기계를 선택해야 할까요?
에픽 파우더 20년 이상의 분말 엔지니어링 전문 지식을 바탕으로 전 세계 첨단 산업에 서비스를 제공하고 있습니다. 또한 유럽 핵심 기술과 비용 효율적인 현지 생산을 결합했습니다. 자체 R&D 및 생산 시설을 통해 신속한 맞춤 제작 및 납품이 가능합니다. 분쇄, 분류, 이송 및 시스템 통합을 포함한 턴키 솔루션을 제공합니다.
파우더로 구동되고 EPIC으로 엔지니어링됨