When designing batteries and selecting materials, many engineers prefer small particle sizes, especially during the research and development stage. Small particles offer several advantages, but they also come with challenges. The smaller the particle, the more difficult it is to manufacture, the higher the cost, and the poorer the processing performance. A more uniform particle size distribution is often preferred. Reducing the particle size (nano-sizing) of lithium battery materials, especially active materials, presents significant advantages and disadvantages that must be considered based on specific application needs (such as energy density, power density, cycle life, or cost). Below is a detailed analysis of these pros and cons.
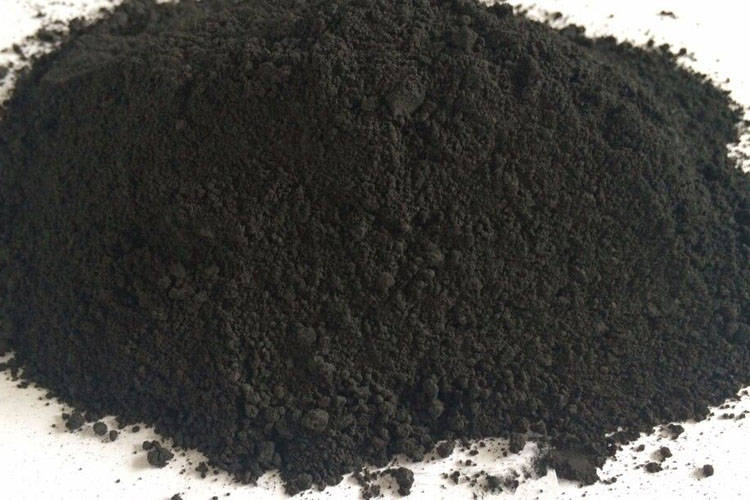
I. Advantages
1. Shortens Lithium Ion Diffusion Path
Small particles reduce the solid-phase diffusion distance of lithium ions within active material particles (from the particle surface to the core).
The benefits include significantly improves rate performance (faster charging and discharging), reduces polarization at high rates and increases power density. This is crucial for power batteries and applications requiring fast charge/discharge capabilities.
2. Increases Specific Surface Area
Smaller particles have a larger surface area per unit mass or volume. More electrode/electrolyte interfaces, accelerating charge transfer and improving rate performance. Closer contact helps build a more complete electronic conductive network, reducing internal resistance. Nanoparticles can better disperse the stress from materials with large volume changes during charging/discharging (e.g., silicon anodes), improving cycle stability.
3. Improves Theoretical Capacity Utilization
Materials with low intrinsic ion/electronic conductivity (e.g., lithium iron phosphate (LFP)) may have incomplete reactions within larger particles. Nano-sizing brings the material closer to fully participating in reactions, allowing it to reach its theoretical capacity.
II. Disadvantages
1. Intensified Side Reactions Due to High Surface Area
A large specific surface area means more contact with the electrolyte, leading to several issues. These consume more electrolyte and active lithium, generate a thicker and more unstable SEI (solid electrolyte interphase) or CEI (cathode electrolyte interphase) film, reducing first coulomb efficiency and accelerating cycle degradation. Side reactions can produce gas, leading to battery expansion, increased internal pressure, and potential safety hazards. A larger active surface may catalyze electrolyte decomposition, compromising the thermal stability of the material.
2. Reduced Tap and Compaction Density
Small particles, especially nanoparticles, have poor stacking efficiency and create more gaps between them. Lower tap density and compaction density reduce the volume energy density of the battery. This presents a challenge for applications seeking high energy density, such as consumer electronics and long-range electric vehicles.
3. Deteriorated Processing Performance
High surface area nanoparticles tend to agglomerate, making them difficult to disperse evenly. This leads to high slurry viscosity and poor stability. Difficulty in electrode coating: High viscosity can make coating uniformity difficult, causing cracks and powder loss. The micropores formed by nanoparticles are smaller and more tortuous, making it harder for the electrolyte to infiltrate the entire electrode, affecting performance.
4. Significantly Increased Costs
Nano-material production (e.g., special grinding, chemical synthesis, spray pyrolysis) is more complex, energy-intensive, and less scalable, leading to higher raw material costs. Additionally, the strict dispersion processes required for these materials add to manufacturing costs.
5. Potential Decline in Electronic Conductivity
The increased contact points between particles (with smaller contact areas) raise the resistance to electron flow between particles. While adding more conductive agents can compensate for this, it can further reduce energy density and increase costs.
III. Summary of Particle Size Considerations
Property | Advantages | Disadvantages |
Reduced particle size (Nano-scale) | Ultra-high rate performance (fast charge/discharge) | Severe interfacial side reactions (low initial efficiency, short lifespan, high gas production) |
High power density | Low tap/packing density (low volumetric energy density) | |
Improved utilization of low-conductivity materials | Difficult slurry dispersion, coating challenges, poor wetting | |
Enhanced cycle life for brittle materials (stress dispersion) | High cost (raw materials & manufacturing) | |
Risk of agglomeration failure | ||
Larger particle size (Micro-scale) | High tap/packing density (high volumetric energy density) | Poor rate performance (slow charge/discharge) |
Minimal interfacial side reactions (high initial efficiency, long lifespan) | Severe polarization under high current | |
Good processing performance (easy dispersion, smooth coating) | Low utilization of low-conductivity materials | |
Relatively lower cost | Prone to fracture for materials with large volume changes – Lithium Battery Industry |
Reducing the particle size of lithium battery materials is a “double-edged sword.” It significantly improves power performance and material utilization, but also introduces challenges such as interface issues, loss of volume energy density, processing difficulties, and higher costs. Pure nanomaterials are rarely used in practical applications. Instead, strategies like particle size grading and surface engineering are employed to strike the right balance between energy density, power density, cycle life, safety, and cost. The ideal particle size range depends on the specific requirements of the battery application.
Conclusion
At Epic Powder Machinery, we are committed to advancing the science and technology of fine powder processing, including the optimization of lithium battery materials. Our expertise in ultrafine grinding and classification technologies helps manufacturers achieve the ideal particle size distribution and material properties for their specific applications. Whether you’re pursuing higher energy density, faster charging, or longer cycle life, Epic Powder provides the equipment and solutions to meet your needs.